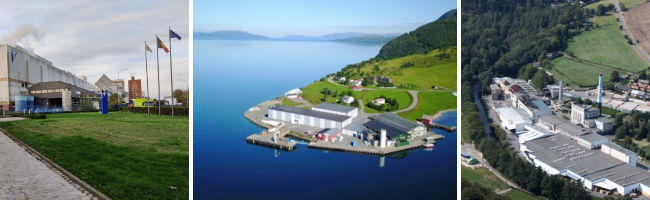
High-temperature heat pumps have found their first movers
This article is a takeaway from the HTHP Symposum 2024, and it gives you the present set-up as the first commercial high-temperature heat pumps have been put into operation, and more are on the way.
Published: April 2024
The first commercial high-temperature heat pumps have been put into operation, and more are on the way. As a part of the SPIRIT Horizon Europe Project, three new industrial high-temperature heat pumps are to be tested in full, commercial scale.
Many companies with a need for process temperatures between 100 °C and 200 °C are now looking at high-temperature heat pumps as one of the technologies that can help them fulfill their Net Zero strategies.
Approximately 40 percent of the industry's need for process heat lies below 200 °C, which is the temperature range where high-temperature heat pumps are expected to be able to deliver heat with sufficient efficiency. At the High-Temperature Heat Pump Symposium 2024 in Copenhagen, several companies told about their plans to connect high-temperature heat pumps to their processes.
- It's all about finding first movers, and fortunately there are quite a few of them. We don't need hundreds of first movers when we can find some of the big players in the industry who want to move first. When the big ones have shown the way with good business cases, the others will follow, said Sander Geelen from Geelen Counterflow – a company that offers drying solutions for the food and feed industries based on heat pumps.
Three SPIRIT projects in 2024
One of these first movers is the Belgian sugar company Tiense Suikerrafinaderij which aims to decarbonize its entire sugar production. Tiense Suikerrafinaderij is a part of Südzucker, which is the world's largest sugar producer.
- We want to follow Science Based Targets, and we are in the process of planning an electrification of our sugar production in order to decarbonize. It's not a choice we have, but a demand from our customers and from the market. Now, we are starting with a 4 MW high-temperature heat pump as a part of the SPIRIT project, said Bart Aerts, Production Manager at Tiense Suikerrafinaderij, at the High-Temperature Heat Pump Symposium 2024.
Sugar beets consist of 10 percent sugar and 90 percent water. Therefore, drying and evaporation are crucial for sugar production. Today, the production at Tiense Suikerrafinaderij is based on fossil fuel, primarily natural gas with a small amount of self-produced biogas and a bit of coal.
- The new heat pump solution is provided by GEA, and the goal is to demonstrate a heat pump system with a screw compressor to generate steam around 139 °C at a capacity of 4 MW. The goal is that the experiences from the SPIRIT project will form the basis for using high-temperature heat pumps in many of Südzucker's 55 factories, said Bart Aerts.
Norwegian prawn production
The SPIRIT project also includes two new industrial applications of high-temperature heat pumps, which are to be tested in full scale and commercial operation. The Norwegian food manufacturer Stella Polaris AS supplies cooked, peeled, and frozen prawns. The current energy supply of steam for the production is a propane boiler with an estimated annual fuel consumption of about 9,000 MWh, corresponding to around 2,600 tons of CO2 per year. Stella Polaris is aiming for an electrified, climate-neutral production and has therefore joined the SPIRIT project. The goal is to demonstrate a high-temperature heat pump based on a screw compressor with hydrocarbon as a refrigerant.
The heat pump will deliver steam temperatures at around 143 °C with a capacity of 1.2 MW and replace the steam produced from the fossil fuel-based boiler. The technology supplier is Mayekawa, a manufacturer of heat pumps for a wide range of temperatures and applications.
Photos: Tiense Suikerrafinaderij (top left), Stella Polaris (top middle/right), and Smurfit Kappa (bottom).
Steam-based packaging production
The third demonstration site for industrial high-temperature heat pumps in the SPIRIT project is in the Czech Republic at Smurfit Kappa – a company that manufactures paper and board for packaging. In the paper industry, steam is used in drying processes, and in this case, the steam is produced with a natural gas boiler with five percent biogas. The annual fuel consumption for this installation is in the order of 353 TJ, which is equivalent to almost 19,000 tons of CO2 per year.
Smurfit Kappa’s ambition is to reduce their dependence on fossil fuels and to reduce their CO2 emissions, and here an electrically driven high-temperature heat pump is a good fit. The technology provider selected by Smurfit Kappa is Spilling, which has a portfolio of steam compression systems that can increase the pressure of excess low-pressure steam and waste/excess steam from the production. The piston compressor produces high-pressure steam (6 bar), delivering 0.7 MW of heat at a temperature of 157 °C to the process at Smurfit Kappa.
Solar energy and heat pumps in Ireland
Another participant at the High-Temperature Heat Pump Symposium 2024 was the tobacco manufacturer Philips Morris International, who also wants to use high-temperature heat pumps in its processes. Philip Morris International has a goal of CO2 neutrality in 2025 and Net Zero in 2040 (Scope 1-2-3). Therefore, the tobacco production needs to be decarbonized in one way or another.
Arjun Arya, Senior Environmental Engineer Lead at Philip Morris International, told that they are working on a pilot project with a 1 MW plant that will deliver steam at temperatures up to 150 °C.
- High-temperature heat pumps are one of the technologies selected for our future processes, including steam production. In our business cases, we operate with an internal CO2 shadow price, which helps to make fossil solutions more expensive, and this will help pave the way for decarbonization, said Arjun Arya.
The Ahascragh Distillery in Ireland is one of the first examples of commercial use of a heat pump, which delivers temperatures up to 115-120 °C. The Irish company Astatine Ltd has provided and integrated the solution, which includes a high-temperature heat pump from the Finnish company Oilon.
To promote a high energy efficiency in Irish heat pump projects, the support rate depends on the COP: the higher the COP, the higher the support. A COP of 3 provides a support rate of 30 percent, while a COP of 4 provides a support rate of 40 percent.
- In some cases, we recommend our customers to combine solar cells and heat pumps. Ireland has the lowest degree of green transition in Europe, so for us, this is a very exciting market, said Tom Marren, CEO of Astatine.
Up the S-Curve
Geelen Counterflow's CEO is very optimistic about the future market for high-temperature heat pumps for drying and cooling.
- The largest customers in our segment of food and feed manufacturers may have 100 drying plants with 2-3 heat pumps on each plant, so these customers have several hundred heat pumps that potentially need to be converted to electrified high-temperature systems. But future developments are very much about standardization. If we are to move up the S-Curve with high-temperature heat pumps, we need standardized solutions, not tailor-made solutions for each new system. You need to find all the identical applications and processes at your customers, and then you can start offering standardized solutions. That's our strategy, said Sander Geelen.
Read the article on LinkedIn